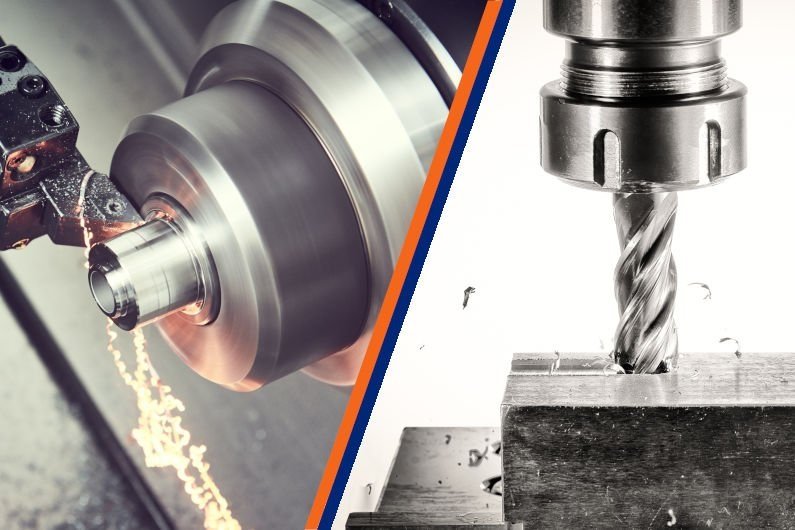
CNC Turn vs CNC Mill Service: What Are the Differences
November 7, 2024CNC technology is essential in processing raw materials into high-quality components with extreme precision. Among the many CNC machining operations, CNC turning and milling are the most popular. While both techniques are necessary for modern manufacturing, they serve different objectives and provide distinctive benefits depending on the project requirements.
CNC turning and CNC milling uses various ways to shape materials. CNC turns a workpiece against a cutting tool to obtain the desired form suitable for making highly precise cylindrical parts. On the other hand, CNC milling removes material using a stationary workpiece and a revolving cutting tool, allowing for the creation of complicated forms and features.
This guide discusses the key differences between CNC turn vs CNC mill and the pros and cons of CNC service.
CNC Turn vs CNC Mill Comparison
Here are some of the main differences between CNC turning and milling:
Tool Features
CNC Turning primarily utilizes single-point cutting tools, which are fixed in position while the workpiece rotates. This setup allows for precise material removal from cylindrical surfaces. The simplicity of the tooling system makes CNC turning highly efficient for tasks that involve repetitive machining of round components. The cutting tool moves linearly along the X and Z axes, providing a straightforward mechanism for shaping parts with consistent diameters and lengths.
In contrast, CNC Milling employs multi-point cutting tools such as end mills, face mills, and drills. These tools are placed on a rotating spindle and can be exchanged based on the machining requirements. The milling machine’s ability to move the cutting tool along multiple axes (X, Y, Z, and sometimes additional rotational axes) enables it to handle complex and intricate tasks. This versatility, however, requires more complex tooling setups compared to turning, particularly when working with multi-axis machines.
Applications
CNC turning is widely utilized in industries where precision cylindrical components are required. It is used in the automobile industry to manufacture parts such as pistons, crankshafts, and gears, all of which require high accuracy and durability. CNC turning is useful for creating turbine shafts and bushings with tight tolerances in aerospace. Furthermore, the medical profession relies on CNC to manufacture precise components such as surgical tools and implants.
On the other hand, CNC Milling is useful for various applications due to its capacity to manufacture complicated forms. Electronics use it to create intricately detailed housings, brackets, and enclosures. CNC milling is often used to manufacture medical devices to produce detailed pieces, such as dental implants and surgical equipment. CNC milling is commonly used in manufacturing to create custom parts and prototypes with various shapes and details.
Machining Operations
CNC Turning involves several key operations. Turning removes material to form cylindrical shapes, whereas facing produces a flat surface at the workpiece’s end. Threading operations can cut internal or external threads, giving cylindrical parts more functionality. These processes are ideal for items that require rotational symmetry and exact diameters.
CNC Milling, on the other hand, includes a variety of operations that enhance its versatility. Face milling cuts flat surfaces on a workpiece, while slotting creates grooves or slots. Profiling allows for the machining of complex contours and 3D shapes. Drilling operations enable the creation of holes of various sizes and depths. These diverse operations make CNC milling suitable for producing detailed and multifaceted components.
Shapes Produced
CNC turning is perfect for manufacturing cylindrical objects like shafts and tubes because of its revolving cutting technique. It can also generate conical objects by adjusting the tool path and cutting angles. The method excels at producing parts with rotational symmetry, which is useful for components that require constant diameters and smooth surfaces.
In comparison, CNC milling may produce shapes other than cylindrical ones. It can machine flat surfaces, complex geometries, and intricate curves. Milling is ideal for parts with asymmetrical characteristics, such as complicated slots, pockets, and 3D profiles. This adaptability enables CNC milling to handle various components and designs.
Compatible Materials
CNC turning can work with various materials, including steel, aluminum, brass, and titanium. It can also machine plastics such as Delrin, acrylic, and nylon. Due to its diversity in material compatibility, CNC turning is an important method for creating components in various industries, including automotive and medical equipment.
CNC Milling also works with a variety of materials. It is widely used for metals like steel, aluminum, stainless steel, and exotic alloys. Milling can be used with plastics such as ABS, polycarbonate, and PTFE, as well as composites such as carbon fibre and fiberglass. This material compatibility enables CNC milling to meet various industrial needs and project specifications.
Pros and Cons of CNC Service
Employing CNC machining services offers several benefits to help achieve business goals. However, there are some limitations that make it less suitable for some applications.
Pros
Here are some of the benefits of CNC machining services.
- High Precision and Consistency: CNC machines produce highly accurate and consistent parts. Computer control ensures that each component meets exact specifications and tolerances, crucial for high-quality manufacturing.
- Efficiency and Speed: CNC machining processes are often faster and more efficient than manual methods. The cutting, drilling, and shaping automation reduces production times and increases throughput, making it ideal for small and large production runs.
- Versatility: CNC machines can handle various materials, including metals, plastics, and composites. They can perform multiple operations, such as milling, turning, drilling, and engraving, which allows for producing complex and detailed parts.
- Reduced Labor Costs: Automation through CNC machines minimizes the need for manual labour. This minimizes labour costs and minimizes human error, leading to higher overall productivity and fewer defects.
- Enhanced Safety: CNC machines operate with minimal human intervention, which reduces the risk of workplace accidents associated with manual machining. Safety features and protocols are built into CNC systems to protect operators and ensure safe operation.
Cons of CNC Machining Services
Despite its many advantages, there are some downsides you must keep in mind.
- High Initial Cost: The purchase and setup of CNC machines can be expensive. Acquiring, installing, and maintaining CNC equipment may be prohibitive for small businesses or startups.
- Complex Programming Requirements: CNC machines require specialized programming skills and software. The initial setup, including creating and verifying programs, can be complex and may require skilled operators or programmers.
- Maintenance and Downtime: CNC machines require regular maintenance to ensure optimal performance. Mechanical issues, software glitches, or tool wear can lead to machine downtime, impacting production schedules and costs.
- Limited Adaptability for Prototyping: While CNC machines are excellent for production runs, they may need to be more flexible and cost-effective than other manufacturing methods for rapid prototyping or small-batch custom work.
- Training and Skill Development: Operators and programmers must be well-trained to handle CNC machines effectively. This requirement can increase costs and time investments for businesses to develop skilled personnel.
Zintilon CNC Service
Zintilon CNC Service stands out in the industry for its commitment to delivering high-quality machining solutions through advanced technology and extensive experience. Here’s a closer look at what sets Zintilon apart:
Advanced CNC Equipment
At Zintilon, we boast of our cutting-edge equipment. We also invest in the latest CNC machines and technology to ensure our operations’ precision, efficiency, and versatility. Our advanced equipment includes multi-axis mills, high-speed lathes, and state-of-the-art inspection tools for handling various materials and complex geometries. This investment in technology enables us to deliver consistently high-quality components, meeting our clients’ exact specifications and requirements.
10+ Years in CNC Manufacturing
With over a decade of experience in the CNC manufacturing industry, Zintilon has built a strong reputation for excellence. Our extensive background in CNC machining allows us to tackle diverse projects with confidence and expertise. Over the years, we have honed our skills and processes to improve efficiency and maintain high-quality standards. This experience ensures we are well-equipped to handle large-scale production runs and intricate custom orders, providing reliable and innovative solutions for our clients’ manufacturing needs.
Customers Review
Our commitment to top -notch quality and customer satisfaction and quality is can also be seen in the positive reviews from our clients. Customers consistently praise Zintilon for our professionalism, reliability, and exceptional machining capabilities. Many highlight our ability to meet tight deadlines and deliver precise, high-quality parts. Our proactive approach to communication and problem-solving also contributes to our strong reputation in the industry. At Zintilon, we value feedback and continuously strive to improve our services to exceed client expectations.
Conclusion
Many manufacturing companies now rely on CNC machines. These computerized machines use pre-programmed software to automate machining operations, making most production processes more efficient, quick, and precise.
CNC milling and turning remain the most common CNC manufacturing processes. While the two techniques share some similarities, their machining methods are far more complex than first appears. As a result, this article examines the distinctions between CNC turning and milling and how they are used to make unique parts.